In the ever-evolving realm of the petroleum industry, where precision and efficiency are paramount, the role of Carboxymethylcellulose (CMC) emerges as a silent yet powerful contributor. This versatile compound, often simply referred to as CMC, has carved a niche for itself in the world of drilling operations, specifically in the context of reducing wellbore friction—a task of significant importance. As we delve into the intricate realm of drilling processes, it becomes increasingly evident that CMC’s attributes hold the potential to revolutionize the efficiency, cost-effectiveness, and environmental impact of oil well exploration.
At its core, Carboxmethyl cellulose stands as a derivative of cellulose, a common component in the structural framework of plants. This chemical compound undergoes modification through carboxymethylation, resulting in enhanced solubility and unique rheological properties. While its applications span across various industries, it is within the petroleum sector that CMC finds a particularly impactful role.
The quest to reduce friction within the wellbore is fueled by the understanding that efficient drilling operations hinge on the ability to minimize wear and tear on equipment, enhance drilling speed, and ensure optimal bit performance. Herein lies the significance of exploring CMC’s potential as a lubricant. By delving into the intricate mechanisms through which CMC functions as a friction-reducing agent, we uncover a realm of possibilities that have the potential to reshape the dynamics of drilling processes.
As we journey through the subsequent sections, we will navigate the multifaceted applications of CMC, shedding light on its role as a viscosity enhancer in drilling fluids, a friction reducer between the drill bit and wellbore walls, a leak-prevention agent, and even a vital component in cement slurry for well completion. These diverse applications paint a vivid picture of CMC’s versatility and underscore its ability to address various challenges within the petroleum industry. Ultimately, the focus remains unwavering—unveiling the benefits of Carboxymethylcellulose as a lubricant in the ongoing endeavor to reduce wellbore friction and enhance the efficiency of oil well exploration.
CMC in Drilling Fluids
In the intricate choreography of oil well drilling, the performance of drilling fluids takes center stage. These fluids, often referred to as drilling muds, are far more than their names suggest—they are complex formulations that serve as the lifeblood of efficient drilling operations. It is within this realm that Carboxymethylcellulose (CMC), with its exceptional properties, emerges as a key player, enhancing the performance of drilling fluids and contributing to the reduction of wellbore friction.
Drilling fluids, in essence, are tailored mixtures designed to fulfill a myriad of functions. From cooling the drill bit and facilitating the removal of rock cuttings to stabilizing the wellbore walls, these fluids are indispensable to successful drilling operations. CMC’s entrance onto this stage brings a distinct advantage due to its ability to serve as a thickening and suspending agent.
A fundamental requirement of drilling fluids is their viscosity, which determines their ability to carry cuttings to the surface and prevent wellbore collapse. Here, Carboxmethyl cellulose shines. As it is introduced into the drilling fluid composition, its unique molecular structure interacts with water molecules, resulting in a noticeable increase in viscosity. This augmented viscosity is instrumental in the suspension of solid cuttings, preventing them from settling at the bottom of the well and ensuring efficient removal.
Moreover, CMC’s role extends to maintaining the structural integrity of the wellbore. The turbulent conditions of drilling can lead to instability in wellbore walls, a phenomenon known as wellbore collapse. By increasing the viscosity of the drilling fluid, CMC reinforces the walls, counteracting the destabilizing forces and minimizing the risk of wellbore collapse. This seemingly simple action is crucial in ensuring the safety and efficiency of drilling operations.
In essence, Carboxymethylcellulose becomes a silent but impactful presence in drilling fluids, lending its viscosity-enhancing and suspending properties to the intricate dance of drilling. By maintaining the proper viscosity, preventing cuttings settlement, and bolstering wellbore stability, CMC plays a vital role in reducing friction within the wellbore. As we delve deeper into subsequent sections, we will unravel how CMC’s capabilities extend further, positioning it as an indispensable lubricant in the quest to minimize friction and optimize drilling processes.
CMC as Friction Reducer
The endeavor to optimize drilling operations transcends the mechanical aspects of wellbore stability and cuttings removal. At its core lies the relentless pursuit of minimizing friction—an adversary that can impede efficiency, increase wear and tear, and escalate operational costs. In this battle against friction, Carboxymethylcellulose (CMC) emerges as a formidable ally, proving its mettle as a friction reducer within the context of drilling processes.
Carboxymethylcellulose‘s role as a friction-reducing agent finds its zenith in the interaction between the drill bit and the wellbore walls. This interaction, fraught with mechanical stress and heat generation, can lead to premature wear on the drill bit and increased energy consumption. It is within this domain that CMC demonstrates its ability to create a lubricious barrier that mitigates friction and facilitates smoother movement.
The mechanism through which CMC reduces friction is both intricate and effective. As it is introduced into the drilling fluid, CMC’s molecular structure undergoes a transformation, forming a protective layer between the drill bit and the wellbore walls. This layer, rich in anionic charges, facilitates a gliding effect, minimizing direct contact between the two surfaces and thereby reducing the frictional resistance.
The significance of this reduction in friction cannot be overstated. By incorporating CMC as a lubricant, drilling operations experience a dual benefit. First, the wear and tear on the drill bit are significantly diminished, leading to extended tool life and reduced operational costs. Second, the reduction in friction translates into less heat generation, ultimately contributing to a more efficient drilling process.
Comparisons with traditional friction-reduction methods further underscore CMC’s prowess. Traditional methods, often involving the introduction of chemical lubricants, can pose environmental and operational challenges. CMC, in contrast, stands as a more environmentally friendly alternative due to its biodegradability and non-toxic nature. This inherent compatibility with eco-friendly practices aligns well with the industry’s growing emphasis on sustainability.
In essence, Carboxymethylcellulose‘s role as a friction reducer is not merely about mitigating mechanical resistance; it’s about enhancing drilling efficiency, prolonging tool life, and contributing to sustainable drilling practices. As we traverse through subsequent sections, we’ll delve into CMC’s multifaceted contributions, highlighting its capacity to address challenges and innovate within the petroleum industry.
Leak Prevention and Hole Sealing
As the drilling process delves deeper into the Earth’s layers, the quest for hydrocarbons encounters a dynamic and challenging environment. One of the crucial challenges is maintaining the integrity of the wellbore, ensuring that the drilling fluid remains contained within the designated path. This is where Carboxymethylcellulose (CMC) steps in, assuming the role of a leak-prevention agent and hole sealer, safeguarding the wellbore and preventing unwanted fluid migration.
Drilling fluids, while pivotal for the drilling process, can pose potential risks if they escape into porous formations surrounding the wellbore. Known as lost circulation events, these occurrences not only lead to a loss of valuable drilling fluid but can also disturb the equilibrium of subsurface formations. CMC’s unique attributes make it an effective solution to address this challenge.
When Carboxmethyl cellulose is introduced into the drilling fluid, its molecules exhibit a fascinating behavior. As the fluid comes into contact with porous or fractured formations, the CMC molecules expand and create a sealing barrier. This barrier effectively bridges the gaps and pores, preventing further fluid migration. The result is a reduction in lost circulation events, leading to fewer operational interruptions, enhanced drilling efficiency, and significant cost savings.
Beyond its role as a leak-prevention agent, CMC also finds application in hole sealing—a process essential for maintaining wellbore stability. As drilling operations progress, the wellbore is exposed to varying pressures, which can lead to the formation of unstable zones. By introducing CMC into the drilling fluid, operators create a barrier that stabilizes these zones, preventing wellbore collapse and maintaining overall wellbore integrity.
The importance of effective leak prevention and hole sealing cannot be overstated. Ensuring that the drilling fluid remains within the designated path not only conserves resources but also prevents potential environmental risks. Moreover, hole sealing contributes to safe and efficient drilling operations, minimizing the chances of wellbore instability.
In essence, Carboxymethylcellulose serves as a guardian of the wellbore, protecting it from potential fluid leakages and maintaining its structural integrity. Its dual role as a leak-prevention agent and hole sealer demonstrates its versatility and underscores its ability to address critical challenges in the petroleum industry. As we journey further, we will uncover yet another facet of CMC’s capabilities—its contribution to environmentally friendly water-based mud systems.
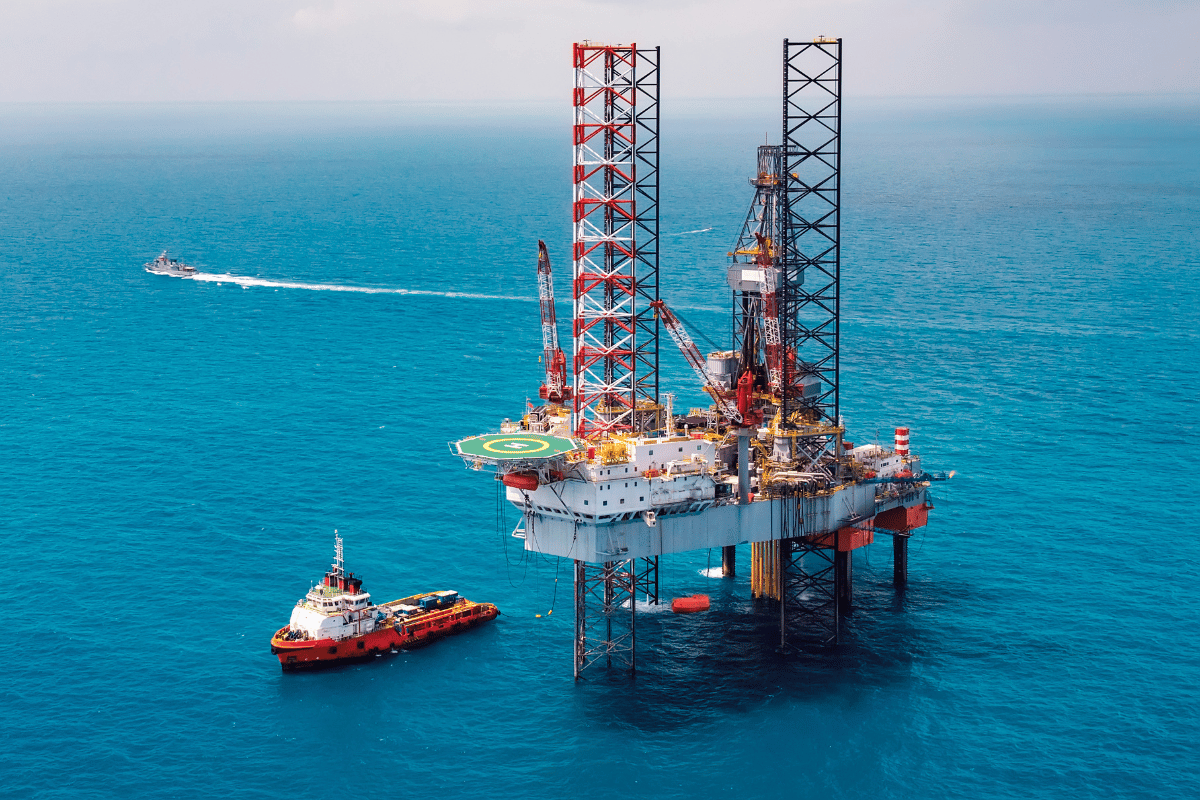
Water-Based Mud and Environmental Impact
In an era where environmental sustainability is at the forefront of global concerns, the petroleum industry is undergoing a transformative shift towards more eco-friendly practices. A pivotal aspect of this transformation lies in the choice of drilling fluids. While traditional oil-based muds (OBMs) have long been a staple, the industry is progressively embracing water-based muds (WBMs) as a greener alternative. At the heart of this transition is Carboxymethylcellulose (CMC), a key player in enhancing the environmental compatibility of drilling fluids.
Water-based muds, as the name suggests, predominantly consist of water, which inherently makes them less toxic and more biodegradable compared to their oil-based counterparts. This aspect aligns well with the industry’s increasing focus on reducing its environmental footprint. Within the realm of WBMs, CMC finds a strategic role that not only enhances fluid performance but also contributes to minimizing the environmental impact of drilling operations.
As a component of water-based mud systems, CMC brings multiple advantages to the table. Firstly, it addresses a significant challenge associated with water-based muds—the need for proper viscosity and stability. CMC’s viscosity-enhancing properties ensure that the drilling fluid attains optimal thickness, allowing it to effectively carry cuttings to the surface and maintain wellbore stability. This is particularly crucial in achieving successful drilling operations.
Furthermore, CMC’s presence enhances the performance of WBMs by contributing to the inhibition of reactive shale formations. These formations, if left unchecked, can lead to wellbore instability, increased operational costs, and even environmental hazards. By forming a protective layer on the wellbore walls, CMC prevents the swelling and disintegration of shales, ensuring the structural integrity of the wellbore and minimizing the risk of environmental contamination.
In the larger context of environmental responsibility, CMC’s integration into water-based mud systems significantly reduces the carbon footprint of drilling operations. The compound’s biodegradability ensures that its presence in the environment does not leave a lasting impact, aligning with the industry’s goals of sustainability and ecological stewardship.
In essence, Carboxymethylcellulose emerges as a linchpin in the transition towards eco-friendly drilling practices. Its incorporation into water-based mud systems not only enhances operational efficiency but also reduces the environmental burden associated with drilling operations. As we proceed, we’ll uncover yet another facet of CMC’s involvement—its role in cement slurry for well completion, a phase critical to the overall success of drilling processes.
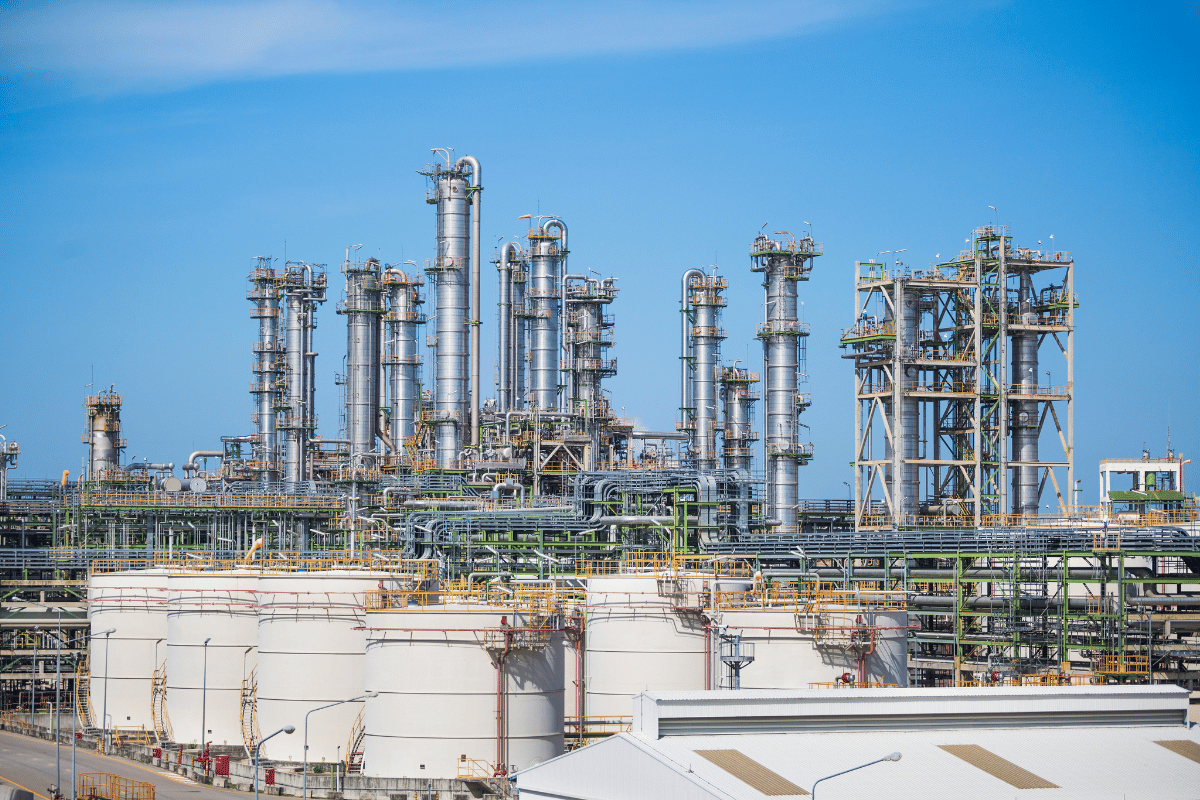
Well Completion and Cement Slurry
As the drilling journey approaches its zenith, the well completion phase takes center stage. This pivotal phase is a culmination of the drilling process, where the wellbore is fortified, isolated, and secured for operational longevity. At this juncture, Carboxymethylcellulose (CMC) reprises its role, this time as a crucial component in cement slurry—a key element in ensuring the structural integrity of the wellbore.
Cement slurry serves as the binding agent that secures the casing within the wellbore, isolating various geological formations and preventing the migration of fluids between them. The composition and placement of this cement slurry are paramount to the success of well completion. It is within this context that CMC’s unique attributes come into play.
Carboxymethylcellulose serves as a thickening agent in cement slurries, transforming them into a well-distributed and stable mixture. As the cement slurry is pumped into the wellbore, the CMC molecules interlock, increasing the viscosity of the slurry. This controlled thickening ensures that the cement remains suspended in the slurry, mitigating the risk of settling and ensuring uniform distribution within the wellbore.
The significance of CMC’s involvement extends beyond viscosity enhancement. It contributes to the overall effectiveness of the cement slurry in two crucial aspects: distribution and solidification. The uniform distribution of cement within the wellbore is essential to achieving wellbore isolation, preventing voids or gaps that could compromise the well’s integrity. CMC’s viscosity-enhancing properties play a pivotal role in ensuring this even distribution.
Moreover, CMC’s role in controlling the solidification process is equally critical. As the cement slurry sets and hardens, CMC’s ability to retain water becomes advantageous. This retained water contributes to proper curing, leading to improved compressive strength and reduced permeability of the cement. These attributes are essential for preventing fluid migration, ensuring well integrity, and prolonging the life of the well.
In essence, Carboxymethylcellulose‘s presence in cement slurries encapsulates its multifaceted contributions within the petroleum industry. From enhancing fluid properties and wellbore stability to ensuring the successful completion of the well, CMC stands as a pivotal component that underscores the industry’s commitment to operational excellence and environmental responsibility. As we move towards the conclusion, we’ll recapitulate the diverse applications of CMC and its overarching impact on petroleum processes.
In the intricate tapestry of the petroleum industry, Carboxymethylcellulose (CMC) emerges as a silent force that reshapes drilling dynamics. Its versatility and adaptability shine through its diverse roles—enhancing drilling fluid performance, reducing friction, safeguarding wellbore integrity, and contributing to environmentally friendly practices. From the initial stages of drilling to the critical well completion phase, CMC leaves an indelible mark on efficiency, sustainability, and operational excellence.
As a lubricant, CMC minimizes friction, prolongs tool life, and optimizes operational costs. Its dual function as a leak-prevention agent and hole sealer ensures wellbore stability and prevents environmental risks. In the pursuit of sustainability, CMC integrates seamlessly into water-based muds, enhancing fluid performance while reducing the industry’s carbon footprint. Lastly, its role in cement slurry solidification secures the well’s future by ensuring uniform distribution and integrity.
In the journey towards efficient, responsible, and environmentally conscious oil well exploration, Carboxymethylcellulose stands as a steadfast partner—a testimony to the synergy between innovation and industry. Its quiet presence speaks volumes, echoing a commitment to progress, sustainability, and the relentless pursuit of excellence within the petroleum sector.
References and Further Reading
- Chen, Y., Liu, L., & Ni, Y. (2016). Carboxymethyl cellulose: preparation and applications. In Cellulose Science and Technology (pp. 129-149). Springer.
- Costa, L. M., Pereira, J. H. O. S., Fernandes, L. S., & Lopes, J. C. (2018). Utilization of Carboxymethylcellulose (CMC) in drilling fluids: a review. Journal of Petroleum Science and Engineering, 170, 48-60.
- Dixon, D. R., & Adamson, J. J. (2019). Eco-friendly drilling fluid technology: a review. Journal of Petroleum Science and Engineering, 178, 832-846.
- Guo, Q., Liu, J., Liu, M., Yao, Y., Lu, X., Zhang, W., & Liu, Z. (2019). A study on the rheological property of oil-based drilling fluids with carboxymethylcellulose (CMC) and nanoparticles. Journal of Molecular Liquids, 274, 509-517.
- Li, H., & Chen, S. (2018). Carboxymethyl cellulose (CMC)-assisted biomineralization of calcium carbonate: mechanisms and applications. Green Chemistry, 20(9), 2033-2048.
- Mehdi, M., & Tabatabaei, M. (2020). An experimental study on the rheological behavior of water-based mud containing carboxymethyl cellulose (CMC) and silica nanoparticles. Journal of Petroleum Science and Engineering, 188, 106906.
- Salehi, S., & Alahyarizadeh, G. (2017). Sustainable drilling fluid formulation using carboxymethyl cellulose biopolymer as a viscosity enhancer. Journal of Molecular Liquids, 241, 306-316.
- Swann, M., Fjaer, E., & Okland, J. (Eds.). (2019). Advanced Well Completion Engineering. Elsevier.
- Bourg, I. C., & Sposito, G. (Eds.). (2017). The Geochemistry of Mineral Surfaces. Mineralogical Society of America.
- Amer, M. (Ed.). (2018). Drilling Fluids Processing Handbook. Elsevier.
- Tiab, D., & Donaldson, E. C. (2016). Petroleum Production Systems. Gulf Professional Publishing.
- Gray, G. R., & Darley, H. C. H. (2018). Composition and Properties of Drilling and Completion Fluids. Gulf Professional Publishing.
Article quoted from:Benefits of Carboxymethylcellulose as Lubricants in Reducing Wellbore Friction