Before we used plastic spoons, the only option was to use metal. As plastic became more popular, it began to take over other forms of the utensil. Plastic now is used in numerous application in the tableware industry.

History:
After World War II, plastic was being more regularly used at homes. By the 1960’s, plastic replaced wood, metal and glass as families saw it as beneficial. Manufactures saw it as being easily disposable and eliminated the need to use water, electricity and manpower to wash them. It also brought a “retro” look to their houses with brightly colored plastics. They came in different shapes and sizes and had different textures and handles. It also was more child friendly being gentle and comfortable to grip.
Originally was created in stainless steel then in plastic.
Who invented it?
Spoons originally came to existence by the Egyptians composed originally of ivory, slate and wood carved with religious symbols. Then it was used in the Shang Dynasty China and Sardinia were spoons were made of bones and bronze. Plastic cutlery however was invented by Alexander Parkes.
When was it invented? 1862
Why was it invented? It was invented for being biodegradable and user friendly. It was disposable and eliminated use of water, electricity and manpower to wash. It could be sold in bulk for cheap prices due its economical manufacturing. It was lighter to hold and less volume. Stainless steel was heavier but was a permanent quality while plastic was disposable trash.

How does the original process differ from the current one?
Before to make a spoon the traditional by way of hand fording a bar of silver is marked up to correct proportions for bowl and handle and then is heated until red hot. It is held with tongs and using a hammer, it is beaten into shape. During the process the piece becomes hard and has to be annealed several times, then worked again to get the final shape. It was cut out of a uniform thickness sheet and then formed to shape.
Blanking: Production begins with rectangular plastic. Large rolls are stamped in individual blanks, which are flat pieces roughly the same shape as the piece to be produced.
Rolling: Through a series of rolling operations, these blanks are graded or rolled to the correct thickness and shapes required by the manufacturer’s flatware patterns.
Annealing: Between operations, the blanks must pass through annealing ovens to soften the plastic for further machine operations. The annealing, done under great heat, must be very accurately controlled so the final piece will be resistant to bending and to nicks and dents when in use
.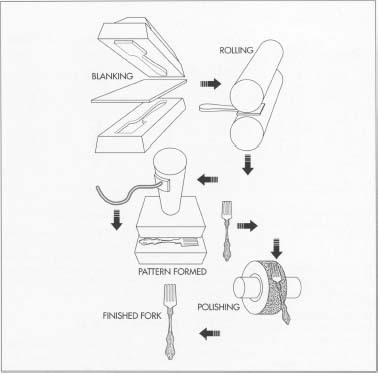
Nowadays in order to make a plastic spoon, there are high tech machines that work efficiently at high speed in order to make in bulk (large quantities). It has complex geometry. They are injection moulded, squeezed under pressure into a precise mould, allowing very precise control of complex geometry.
II) Industrial Process behind the Making
What technique/machines are used to produce it today?
Thermoplastic production begins with ordinary crude oil. The oil is first distilled to separate out its different components, some of which are treated in a process of steam cracking. In steam cracking, the oil distillate is mixed with steam and then heated in the absence of oxygen, to create smaller light molecule in the family of olefins, including ethylene and propylene Olefins are monomers, the fundamental building block from which plastics are made.
The polymer chain are manufactured into resins (a sticky flammable organic substance, insoluble in water) similar to one of a plant which are basic commodity of plastic industry. These resins are subsequently processed into cylindrical pellets which are supplied to product manufacturing companies. These pellets are small, rounded, compressed mass of plastic.
The pellets are melted and fed into a forming process such as extrusion to produce a finished product. Because the properties of the polymer are mainly determined by their chemistry, this last stage of production is entirely about geometry so plastic is efficiently moulded into the finished shapes. The energy need to make plastic varies very little between different types and is around 80MJ/kg and are usually made from oil.

Injection moulded, squeezed under pressure into precise mould while metal is stamped out a sheet. Today it is made from oil but there are different routes which create diverse plastics.
III) Environmental Impact: What is the impact that the material or its process of making have on the environment? Is the process of manufacturing environmentally safe?
Plastic spoon is made from petroleum and estimates are that it can take somewhere between 10 and 100 years to decompose. And when it is decomposing it’s releasing toxic substances into the soil and groundwater.
It is recyclable. The waste management infrastructure currently recycles regular plastic waste, incinerates it, or places it in a landfill. Mixing biodegradable plastics into the regular waste infrastructure poses some dangers to the environment. Biodegradable plastics behave differently when recycled, and have the potential to negatively influence to human health. To be effective in food packaging, plastics must exhibit gas permeability, chemical resistance, and tensile strength. If the food packaging materials are recycled, their physical properties could change, allowing degraded chemical compounds and external contaminants to enter the food. On top of that, plastics contaminated with food are difficult to recycle, and blended plastics sometimes leave behind starch residues that can further contaminate the recycling process. Another option for biodegradable plastic waste is incineration with energy capture, so that the energy that goes into producing the plastic could be reclaimed during decomposition. However, incineration of biodegradable plastics does not create any more energy than petroleum-based plastics, so the environmental effects of the two are roughly equivalent. The third option is landfilling biodegradable plastics. However, when biodegradable plastics decompose, they produce methane gas, a major contributor to global warming. While methane gas could be collected and used as an energy source, capturing that energy would be another expense, and some of the gas would still escape. Thus, the biodegradable nature of these plastics poses economic and ecological problems in the current waste management infrastructure.